Diesel Generator
Patented American Technology
Full Compliance with Emission Standards
End-to-End Expert Support
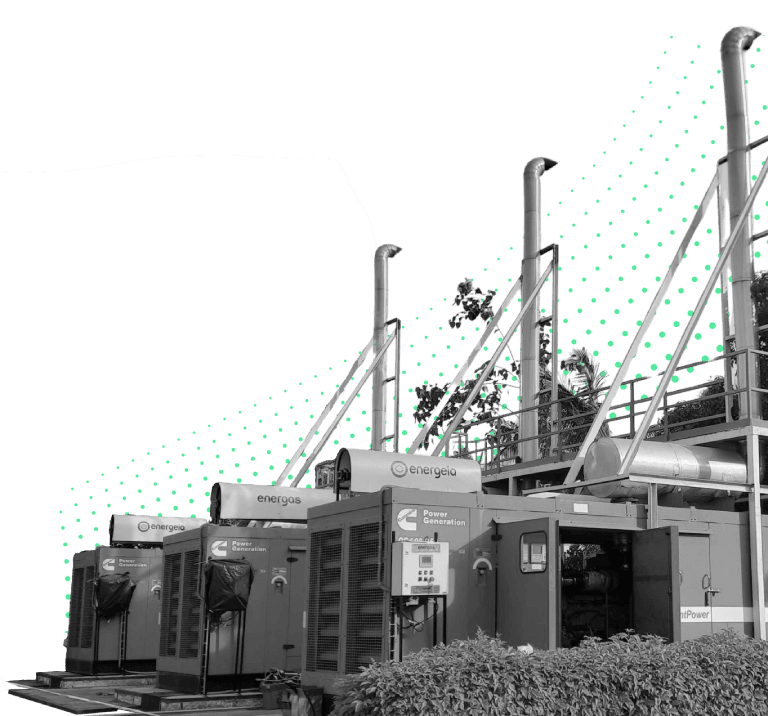
Trusted by Top Companies
Dual Fuel Kits
Convert Your DG to Natural Gas
Pollution Compliance
Comply with your latest State Pollution Control Board Order to avoid fines and DG bans.
Cost Savings
Replace up to 70% diesel with cheaper natural gas, reducing fuel expenses.
Reduce Carbon Footprint
Cut CO₂, NOx, and particulate emissions to comply with government regulations.
Improve Efficiency
Get peak performance with piped gas, extending DG runtime without frequent refueling.
800+ Successful Dual Fuel Kit Installations
Our EnerGas dual fuel kits are the most widely tested and deployed technology on diesel generators across the world.
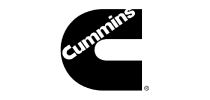
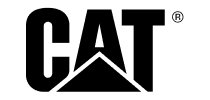
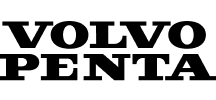


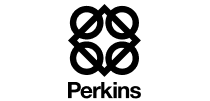
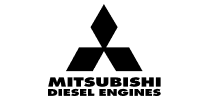
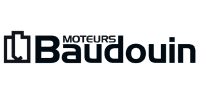
AMERICAN TECH MADE IN INDIA
Breakthrough Partnership
Energeia secured an exclusive technology transfer with GFS Corp, the American inventor and patent-holder of the latest bi-fuel technology, enabling us to develop the most sophisticated dual-fuel EnerGas kits most cost-effectively.

X
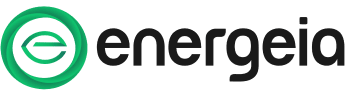
the technology
How the Dual Fuel Kit Works
Natural Gas first enters the Gas Train, where it is filtered, pressure-regulated, and safely supplied to the Integrated Throttle Body (ITB).
The ITB optimizes gas flow to the Air Gas Mixer (AGM), a patented device that ensures a lean air-to-gas ratio at the generator's air inlet. This mix reduces the diesel needed for combustion.
1
Gas Train
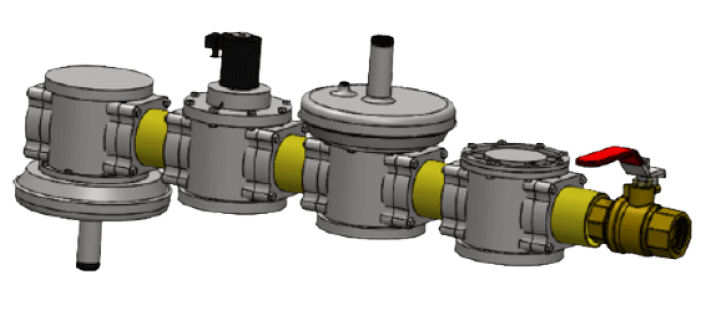
Pressure and Gas Quality
The Gas Train filters and regulates natural gas pressure, ensuring a clean, safe supply to the Integrated Throttle Body (ITB) and the Air Gas Mixer (AGM).
2
PLC
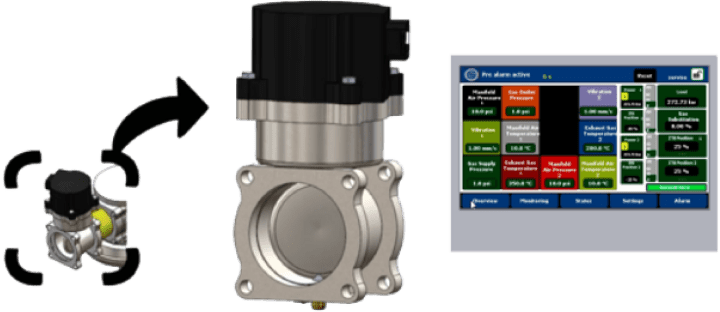
Gas Control Algorithm
The PLC manages the dual-fuel kit by monitoring sensors and optimizing natural gas flow from the Gas Train and ITB using a gas control algorithm.
3
AGM & ITB
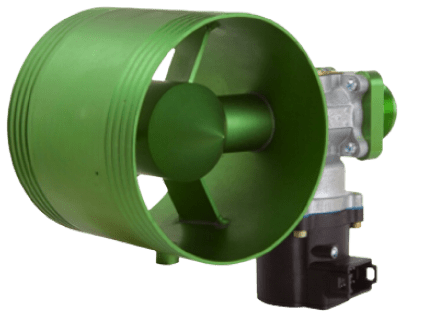
Precise Air-Fuel Ratio Management
The ITB controls gas flow to the Air Gas Mixer (AGM), a patented device attached to the generator's air inlet, ensuring a lean, optimal air-to-gas ratio.
4
IoT Monitoring
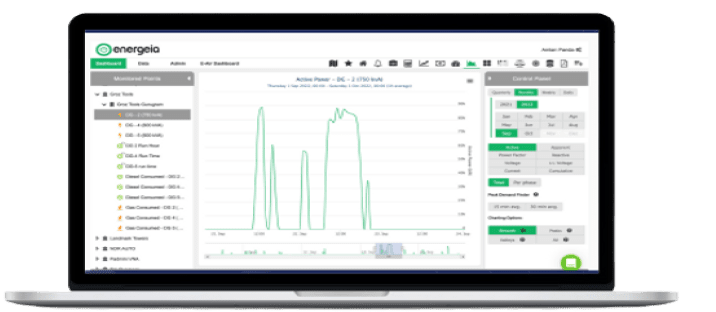
Monitor and Protect
The Integrated IoT Monitoring System tracks performance and alarms in dual-fuel kit installations, enabling proactive maintenance by predicting issues before they occur.
Optimal Gas Substitution
Adaptive Gas Control System
It uses the Integrated Throttle Body (ITB), precisely programmed for each engine and site, with the PLC continuously optimizing ITB position for gas substitution across 15% to 100% engine load.
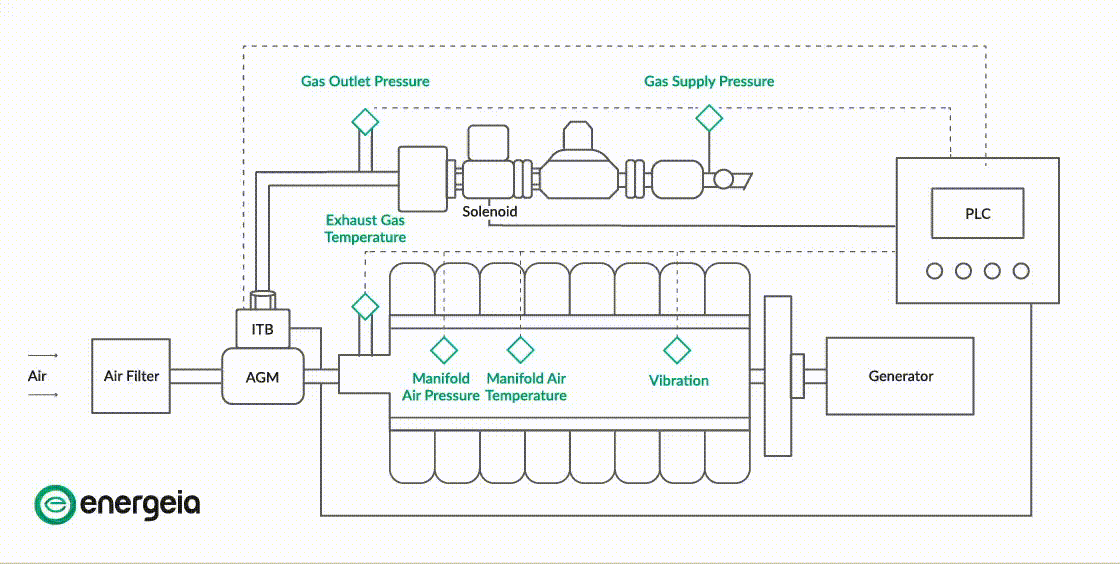
Maximize Diesel Substitution
Diesel Displacement Rate
The dual fuel kit maintains high diesel substitution across the engine load curve (15% to 100%) by adjusting gas usage, ensuring consistent dual fuel operation at any load.
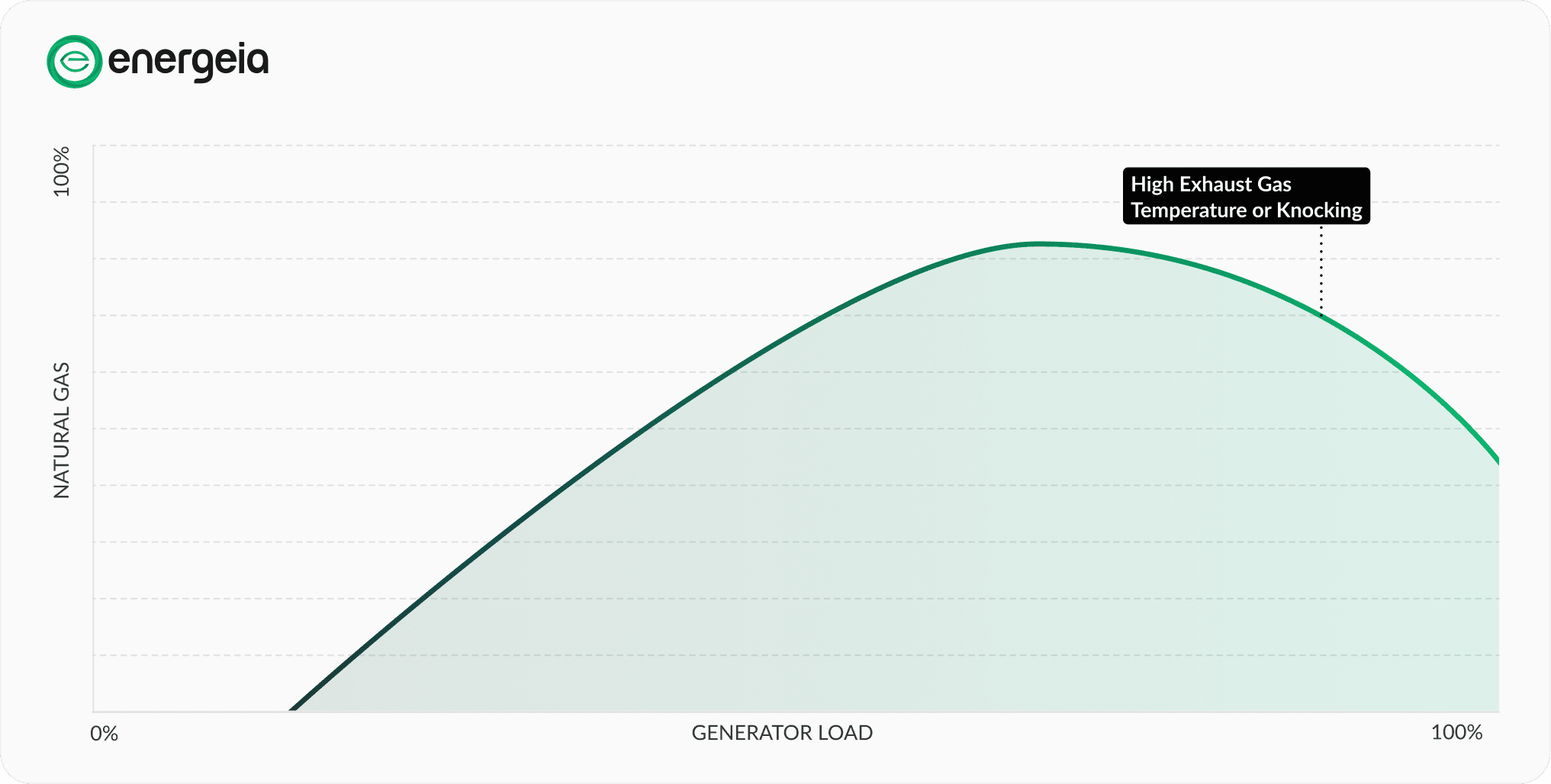
Dual-fuel Conversion
Your Partner, from Start to Finish
1
Assessment
Assess your existing diesel generators, evaluating compatibility and engine health
2
Installation
Retrofit genset to bi-fuel with minimal downtime and trained installation engineers
3
Commissioning
Ensure the dual-fuel kit is running properly and all engine parameters are within range
4
After-Sales Support
Train your plant engineers to operate dual-fuel gensets, and keep us on speed dial for support.
Compliance
Government Compliance for Diesel Generators
There are now mandatory regulations for diesel generator compliance across multiple Indian states to reduce emissions and meet environmental standards.
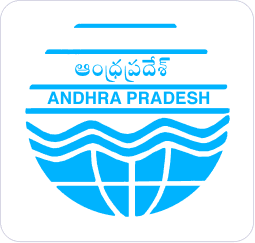
Authority
Andhra Pradesh Pollution Control Board
Date: 01 Nov, 2020
Deadline: 05 Mar, 2021
Regulations
Diesel Generators in commercial buildings and factories must be converted to Dual Fuel (Partial Gas) or installed with an RECD (Retrofitted Emission Control Device) or be completely replaced by Gas generators.
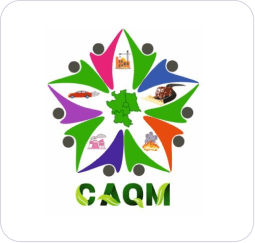
Authority
Commission for Air Quality Management (CAQM)
Date: 29 September, 2023
Deadline: 31st December, 2023
Regulations
Diesel Generators in commercial buildings and factories must be converted to Dual Fuel (Partial Gas) or installed with an RECD (Retrofitted Emission Control Device) or be completely replaced by Gas generators. During GRAP, this regulation extends to all diesel generators, including the ones in residential areas.
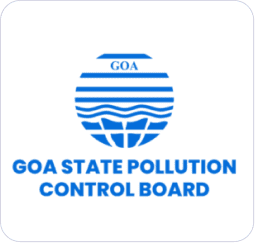
Authority
Goa State Pollution Control Board
Date: 27 August, 2021
Deadline: 06 January, 2023
Regulations
Diesel Generators in commercial buildings and factories must be converted to Dual Fuel (Partial Gas) or installed with an RECD (Retrofitted Emission Control Device) or be completely replaced by Gas generators.
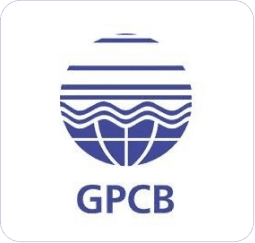
Authority
Gujarat State Pollution Control Board
Date: 26 Oct 2023
Deadline: 26 Apr 2024
Regulations
Diesel Generators in commercial buildings and factories must be converted to Dual Fuel (Partial Gas) or installed with an RECD (Retrofitted Emission Control Device) or be completely replaced by Gas generators.

Authority
Karnataka State Pollution Control Board
Date: 12 June, 2024
Regulations
Diesel Generators in commercial buildings and factories must be converted to Dual Fuel (Partial Gas) or installed with an RECD (Retrofitted Emission Control Device) or be completely replaced by Gas generators.
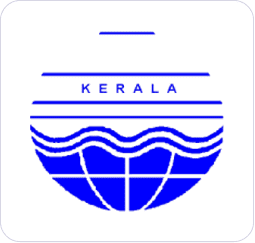
Authority
Kerala State Pollution Control Board
Date: 26 Oct 2023
Deadline: 26 Apr 2024
Regulations
Diesel Generators in commercial buildings and factories must be converted to Dual Fuel (Partial Gas) or installed with an RECD (Retrofitted Emission Control Device) or be completely replaced by Gas generators.
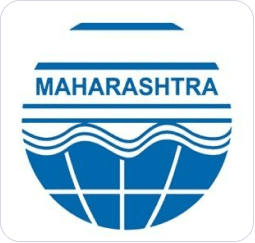
Authority
Maharashtra Pollution Control Board
Date: 2 June, 2023
Deadline: 2 Oct 2023
Regulations
Diesel Generators in commercial buildings and factories must be converted to Dual Fuel (Partial Gas) or installed with an RECD (Retrofitted Emission Control Device) or be completely replaced by Gas generators.
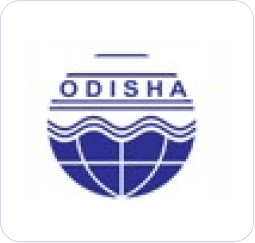
Authority
Odisha State Pollution Control Board
Date: 14 Nov 2023
Deadline: 14 May 2025
Regulations
Diesel Generators in commercial buildings and factories must be converted to Dual Fuel (Partial Gas) or installed with an RECD (Retrofitted Emission Control Device) or be completely replaced by Gas generators.
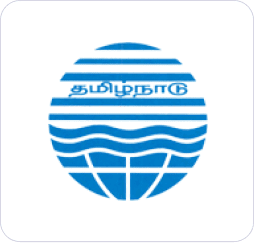
Authority
Tamil Nadu Pollution Control Board
Date: 30 July, 2024
Deadline: 30 Dec, 2024
Regulations
Diesel Generators in commercial buildings and factories must be converted to Dual Fuel (Partial Gas) or installed with an RECD (Retrofitted Emission Control Device) or be completely replaced by Gas generators.
Energeia in Action
faq
All Your Dual Fuel Questions Answered
How much downtime is needed for system installation?
Typically, installation requires 4-6 hours per diesel generator. The system is designed as a stand-alone external solution, with only a minor modification to the generator’s air inlet. This setup minimizes downtime, allowing for a quick and efficient installation without disrupting operations.
Will the Dual Fuel Kit reduce the Diesel Generator's capacity (derating)?
No, the Dual Fuel Kit does not affect the generator’s power output or capacity. It maintains the same performance levels as before the conversion, ensuring that the generator operates efficiently without any derating or loss of power.
What are the Natural Gas (PNG) pressure requirements for the Dual Fuel Kit?
The required natural gas pressure ranges from 1 to 4 bar. For other gas pressures or types like LPG, biogas, or LNG, customized solutions are available. This flexibility ensures that the system can accommodate various gas supplies while maintaining optimal performance.
What is the gas consumption on an hourly basis for different DG capacities?
Gas consumption depends on the engine load and capacity. For example, a converted 500 kVA generator typically consumes around 80 SCM/hr, while a 1010 kVA generator may use up to 150 SCM/hr. Consumption rates will vary according to engine load and operating conditions.
Is there any certification required once I’ve installed a Dual Fuel Kit?
No specific certification is needed, as dual fuel technology is recognized as safe and effective by the Ministry of Environment and Forest, NGT, CAQM, and SPCBs. Energeia provides a Commissioning Report, which you can submit to your state pollution control board as proof of compliance with emission standards.
How long has Dual Fuel Technology been in use and when was it introduced in India?
Dual Fuel Technology has been in use globally for over 40 years, initially developed for oil rigs to utilize flared gas in DG sets. It was introduced in India around 2008, following the availability of natural gas. Energeia has since installed over 800 dual fuel kits across various generator sizes in India.
What happens to the engine if the Dual Fuel Kit fails?
If the Dual Fuel Kit encounters a fault, the system automatically switches back to 100% diesel operation, ensuring uninterrupted performance. The system includes pre-alarms and fault alarms, and any issue triggers a notification to Energeia’s service team, who will respond within 48 hours to address the problem.
Where should the Dual Fuel Kit be installed on a DG set, and does it require major or minor modifications?
The Dual Fuel Kit is installed with minimal modifications, mainly involving the installation of an Air Mixer before the turbocharger, connecting it to the gas train and fuel control valve. This retrofit solution is plug-and-play, requiring no alterations to the engine’s core design or critical parameters.
What measures are taken to ensure the safety of a DG set after its conversion to Dual Fuel?
Safety is ensured by controlling real-time gas injection using a position-controlled gas governor, which responds within 10-15 milliseconds based on engine parameters. Continuous monitoring of load, exhaust temperature, and vibrations, combined with a PLC-based closed-loop control system, ensures safe and efficient operation.
Which types of generators are compatible with the Energas Dual Fuel Kit?
The Energas Dual Fuel Kit is compatible with high-speed diesel engines (1500 RPM) ranging from 62.5 kVA to 3000 kVA. It works with brands like Cummins, Volvo Penta, Kirloskar, Perkins, Mitsubishi, Caterpillar, MTU, and Baudouin. Small-capacity generators below 62.5 kVA are not feasible due to the lack of turbocharging mechanisms.
Related Services from Energeia
Dual Fuel Kits for Mining
Reduce diesel costs and emissions by retrofitting generators to run efficiently on gas using our dual fuel kits.
Utility Optimization
Optimize industrial utilities like air compressors, chillers, and boilers to reduce energy costs and emissions with zero upfront investment.
Energy Audits
Explore more opportunities for sustainability and cost reduction with our customized energy audit services.
Expert Consulting
Achieve your sustainability and cost reduction goals with tailored expert advice for your unique needs.